About OME International
Success Stories
Success Story: Medical Part
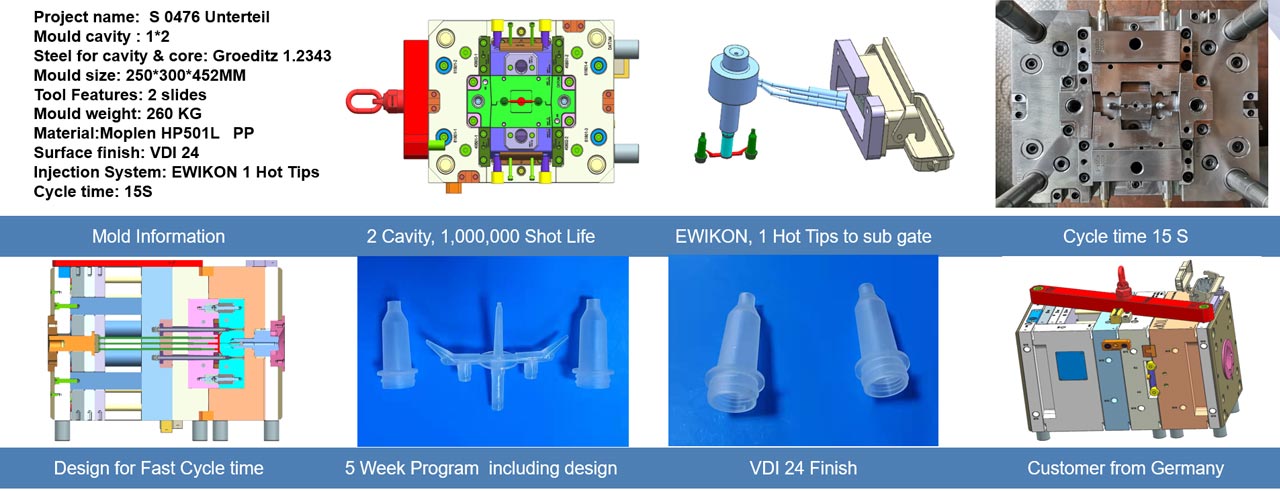
Success Story: 5 Second Cycle
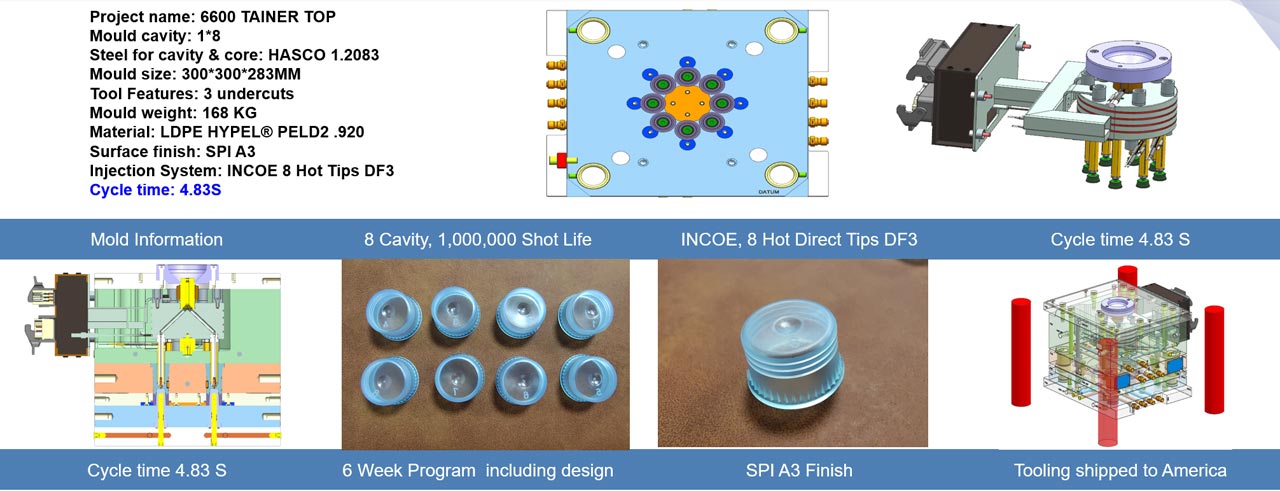
Success Story: 2-Shot Medical
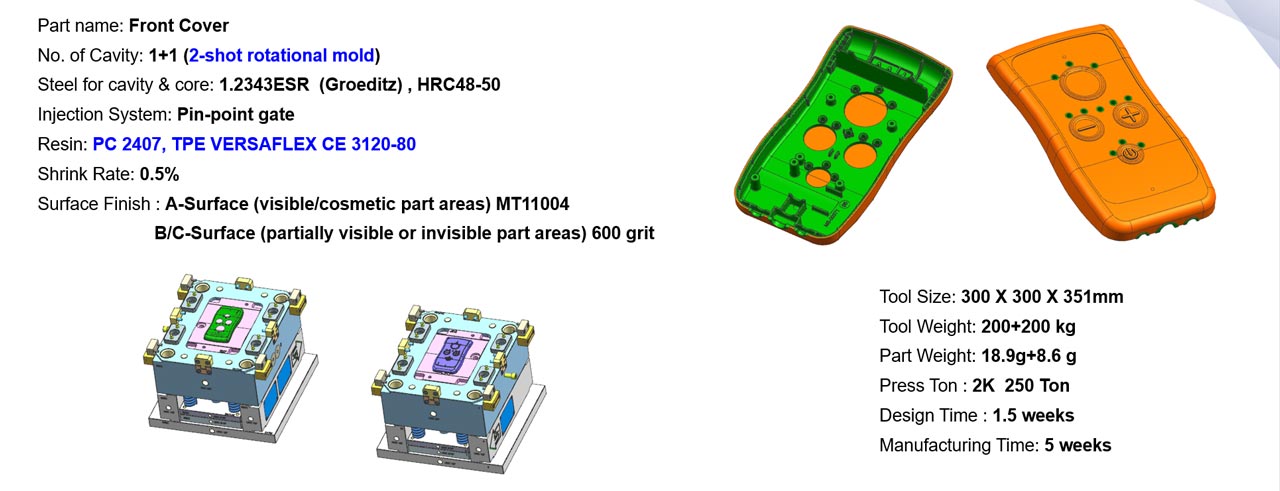
Success Story: Assembly of Manifold Top
OME build all 4 tools and supplies the subassembly to final customer in Israel.
We can help our customers by supplying single molded parts or by providing assembly services.
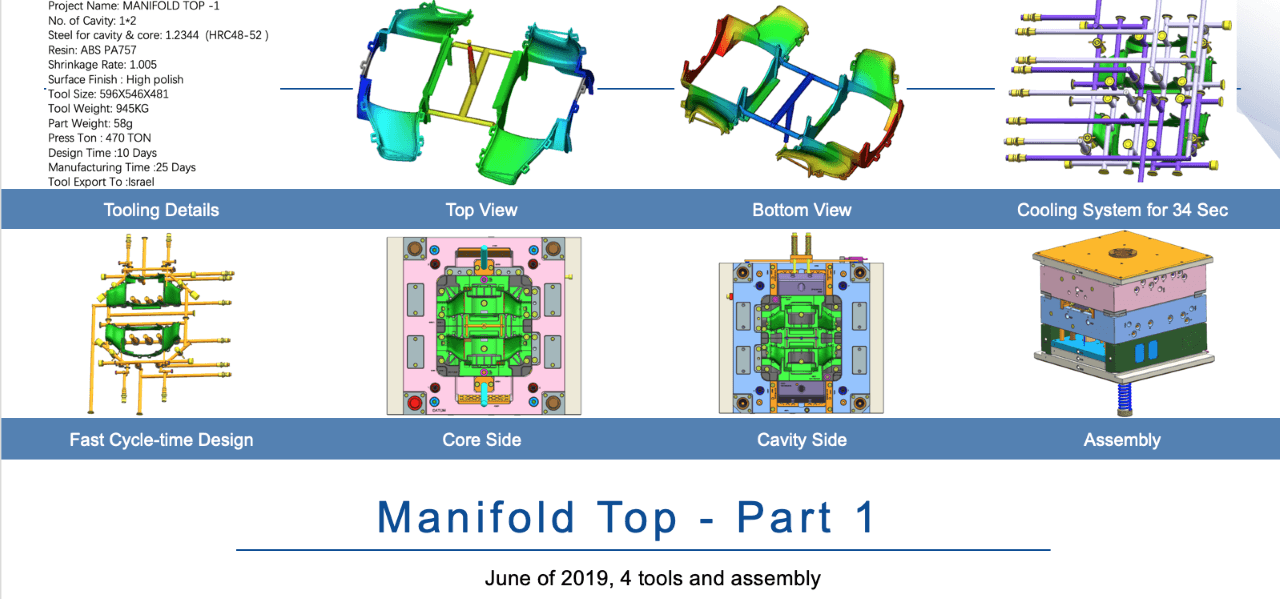

Success Story: 2K Rotational Success
Part name: Car brand lamp
No. of Cavity: 1+1, (2-shot rotational mold)
Steel for cavity & core: 1.2343ESR (Groeditz) , HRC50-52
Injection System: Hotrunner connector configuration (INCOE)
Resin: ABS/PC & PC
Shrinkage Rate: 0.55%
Surface Finish : A-Surface (visible/cosmetic part areas) 1000 grit
B/C-Surface (partially visible or invisible part areas) 600 grit
Tool Size: 396 X 446 X 375mm
Tool Weight: 400 kg
Part Weight: 8 g
Press Ton: 110 Ton
Design Time: 2 weeks
Manufacturing Time: 5 weeks
Export: Germany, December 1, 2018
Success Story: Automotive Light Housing
December of 2018, complete program in 8 weeks including design and adjustments after T1. Program shipped to Germany for production after Trial 2.
Our recommendations resulted in elimination of distortion during ejection and reduced cycle time.